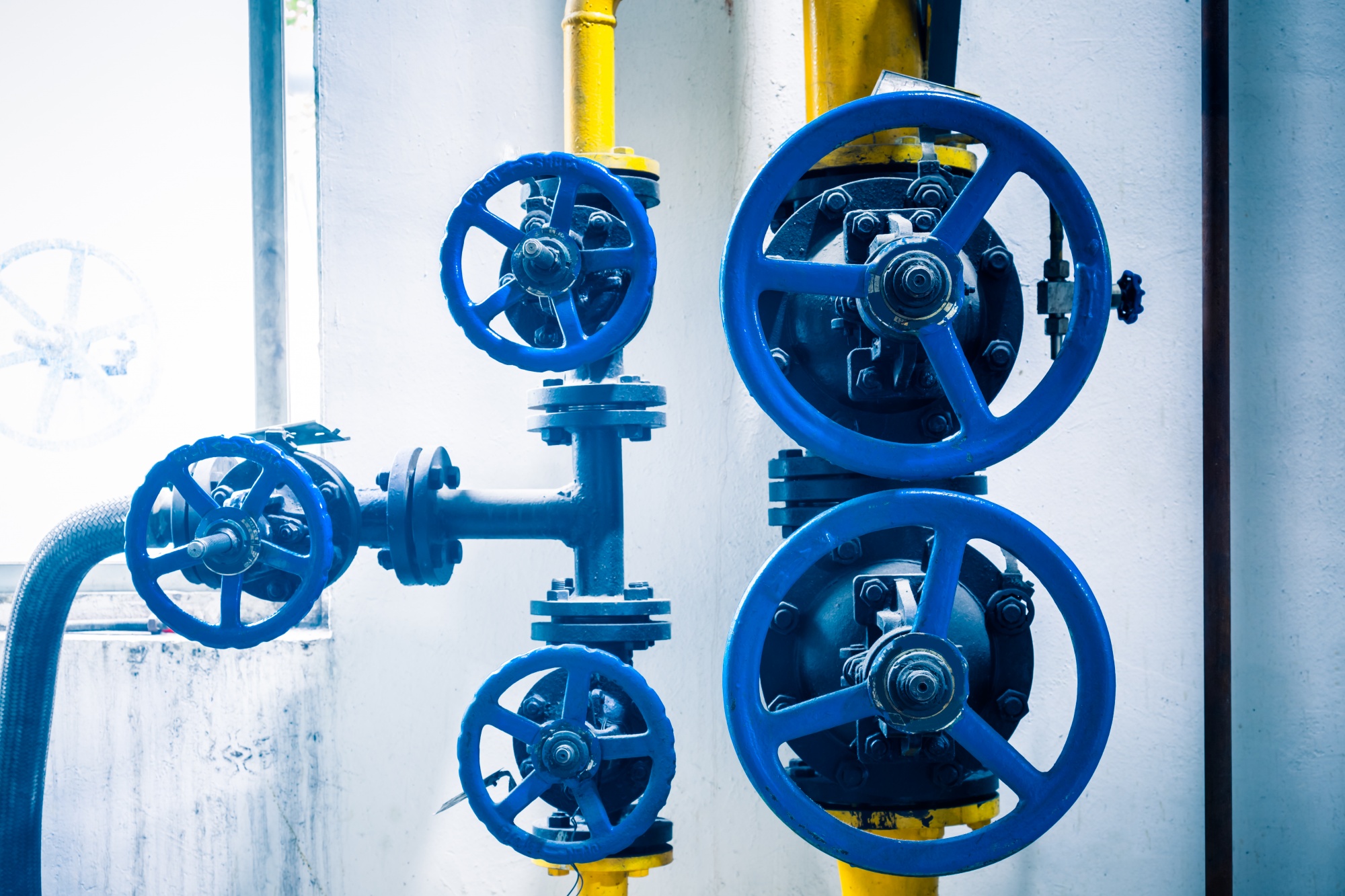
CASTING FACILITY
The casting facility is the department within a valve manufacturing plant responsible for transforming molten metal into various valve components. It plays a crucial role in ensuring the quality, consistency, and cost-effectiveness of the final product.
Here’s a breakdown of the key functions of a casting facility:
Melting: High-temperature furnaces, like induction furnaces, are used to melt the raw metal based on the specific valve design requirements.
Molding: Molds are prepared using various techniques like sand casting or investment casting. These molds create the desired shapes for the molten metal to solidify into.
Pouring: The molten metal is carefully poured into the prepared molds.
Solidification: Once poured, the metal is allowed to cool and solidify within the mold, taking on the desired shape of the valve component.
Cleaning and Finishing: Once solidified, the castings are removed from the molds and cleaned of any residual materials or imperfections. This might involve processes like shot blasting or grinding.
- In-house pattern shops, modern machine shop and testing
- In-house facility backed by generator
- Wind Power for non-stop production
- Installed capacity 3,600 tons per year
- Maximum single piece weight 2,100 kg
- Pattern Shop
- Pattern shop features highly trained pattern makers from the simple to the extremely complex casting design.
- Our patterns ensure accurate casting that meets customer specifications.
- CNC machined patterns provide close & consistent casting tolerances.
- The pattern shop is strengthened with dedicated CNC machine for full time pattern making from solid models and simulation software SOFT CAST 3.5 for methoding.
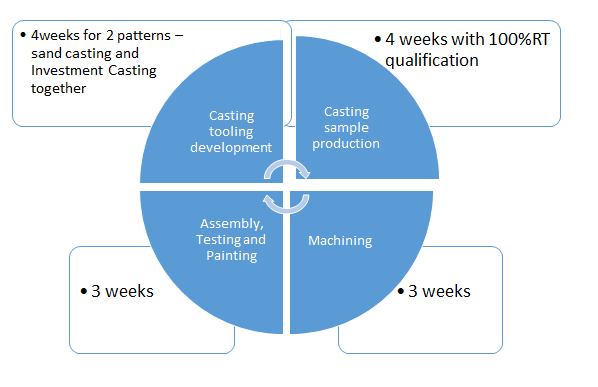
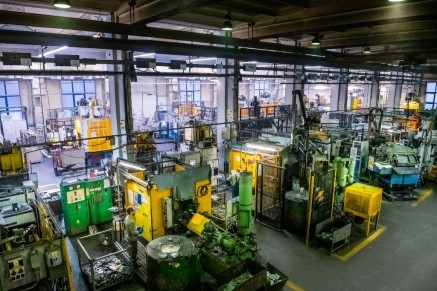